Nanoengineering is often limited by the divide that separates concept from reality, with promising theoretical designs falling short in application. However, a Northwestern University research team led by Sinan Keten is working to bridge this gap as it concerns one particular nanomaterial — cellulose nanocrystals, often termed CNCs.
Capturing CNCs is not the problem. They are nothing new to nature, found naturally within trees. CNCs currently on the market — mostly for research purposes — are extracted directly from wood pulp, a byproduct of the paper industry. They are accessible and relatively easy to extract, nontoxic and biodegradable. The challenge comes in what is lost in translation between the nanoscale and the bulk scale — as these tiny components are fabricated into macroscopic technology such as glass or body armor, their properties might change. A recent paper describes the modeling framework that the Keten lab has been developing. The framework could allow us to design better functional materials from cellulose nanocrystals, by predicting how physical and chemical properties might change in the process.
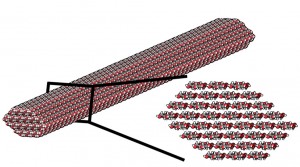
A cellulose nanocrystal’s mechanical properties, including strength and transparency, make it an ideal replacement for synthetic products. As a promising alternative to the Kevlar used in bulletproof glass and body armor, CNCs have already received significant federal research funding. While CNCs can be used alone as thin coatings and flexible films (in food packaging, for instance), they really shine when they are integrated into composite materials.
More broadly speaking, then, CNCs could be used in any product employing polymer composites — materials made of multiple chemical components with differing chemical or physical properties, such as those used in car and airplane frames. Unfortunately, CNC use up to this point has been limited to academic research because accurately predicting the properties of nanocomposite materials is challenging. While scientists are currently capable of producing composites and materials that show promising mechanical properties, research unraveling these properties is scarce.
This is where Keten’s lab enters the scene. “The key bottleneck is that the properties they’re exhibiting fall short of what we would predict to be the optimal performance,” said Robert Sinko, a PhD candidate in the Keten lab. “That’s where our research comes in.”
To better produce materials from CNCs, Keten, Sinko, and other colleagues are developing frameworks to foreshadow a composite’s properties at the bulk scale, factoring in the chemical and physical characteristics that particles exhibit at the nanoscale. Thus far, their model has made significant breakthroughs in accurately predicting glass transition temperatures, where CNC materials transition from a hard, glassy state to a rubbery, soft one.
The model has also helped determine the ideal molecule size for CNC composites. In fact, when the researchers used the model to predict the size at which cellulose nanocrystals best resist fracturing under pressure, they found that the strongest CNCs were between 4.8 and 5.6 nanometers thick, between 6.2 and 7.3 nanometers wide, the dimensions most commonly found in nature. In effect, though the model was intended to improve CNC development for industrial materials, it has also managed to explain why the crystals naturally tend towards certain characteristic dimensions.
While the work of the Keten lab is exclusively computational, partnerships with other research groups have enabled the lab to test the model’s real-world accuracy. “It’s really important to connect with experimentalists that actually confirm some of our hypotheses and help us design better tools,” Keten said. “We work with experimental groups at Northwestern that can mechanically test interfaces between nanocellulose and polymers, which is important for nanocomposite design.” These partnerships will help troubleshoot the model by establishing where computed, theoretical outputs differ from characteristics of real CNC materials.
The Keten lab plans to branch out from a specific focus on a subset of CNC characteristics, namely glass transition temperature, to a wider variety of properties. The team hopes to overcome a challenge in describing the bulk mechanical behavior of composite systems, especially fracture strength and toughness. In addition, the group aims to better understand the relationship between chemical and physical properties of the nanocomposite.
The recent study, published in Nano Letters, and the development of a working model for nanocomposites has poised us to further close the gap between theory and reality in engineering.
“You’re taking a material, in this case pulp from wood, that’s used ordinarily in our lives, and turning it into something quite extraordinary,” Keten said of nanocellulose. Improving the utility of a new class of polymers could lead to better, and perhaps more environmentally sound technology.
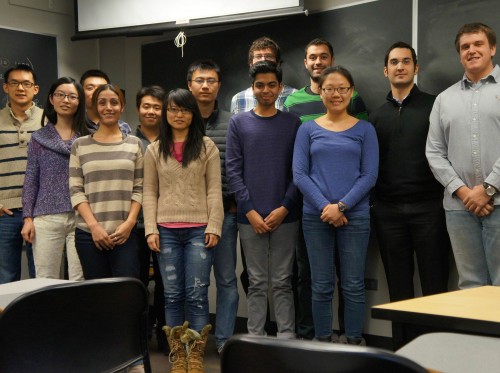