The future of portable power and renewable energy will likely be driven by electrocatalytic devices, such as fuel cells and metal-air batteries. These devices, which convert the chemical energy of a fuel like hydrogen into electricity, have such applications as fuel cell–based vehicles that would run on compressed hydrogen gas. These autos would produce half the amount of greenhouse gas emissions that are made by vehicles running on fossil fuels. But the widespread commercial development of electrocatalytic devices is hampered by their high cost. The noble metal catalysts (like palladium) used to drive the transformation of chemical fuel into electricity are expensive and rare.
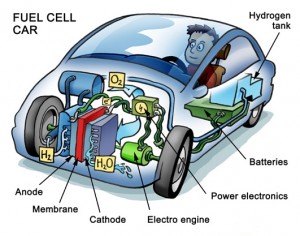
To address the cost issue, a team of Yale University researchers investigated how to make the catalytic structures at the core of devices like fuel cells cheaper and more efficient. Noble metal catalysts need to be embedded into a larger structural support in order for electrocatalytic devices to work; the chemical reactions that they catalyze happen on the surfaces of these structures. The team, which was led by professor of chemical and environmental engineering Andre Taylor, was the first to use a material known as bulk metallic glass (BMG) to create the catalytic surface.
BMGs are ideal materials: composed of noble metal catalysts and other metals like silicon, they are both strong and extremely amorphous. “You can heat [a BMG] up, form it, and cool it down, Taylor said. “It will once again have all the properties of a metal, including strength.” Because of these properties, BMGs can be stretched into tiny wires—only a few nanometers thick—with relative ease. A surface composed of millions of tiny wires has a much higher surface area than a smooth one. This allows more catalytic metals to come into contact with the chemical fuel, which increases reaction efficiency.
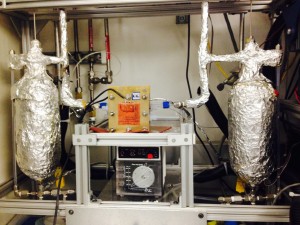
The team, which also included Ph.D. candidate Jinyang Li, also sought to fine-tune the BMG material itself. To uncover additional noble metal catalysts, they removed some of the non-noble metal atoms from the surface of the BMG nanostructures. Micro-pores in the structure’s surface are left behind, further increasing the surface area on which reactions can occur.
Though BMGs have incredible potential, there are other electrocatalytic components—like energy-storing capacitors—that are more efficient when made of non-BMG materials. Typically metals, these materials are less moldable than BMGs and thus are extremely difficult to sculpt into nanostructures. By using additive processes involving electric fields, the team found they could give the BMG nanostructures a metal coating. With this technique, scientists could create nanoshapes with a BMG and simply spray the desired metal onto it. For example, Taylor’s team coated BMG nanorods with manganese oxide to create a highly efficient pseudocapacitor.
While these methods are still too expensive to be deployed commercially, they significantly advance the study of electrochemical surfaces. The team’s discovery will be the cover story for the magazine Advanced Materials. The featured image—a stunning graphic of interlaced nanowires—might offer a glimpse into the future of energy.